Formlabs form3
Formlabs form3 es una solución para fabricar moldes de inyección rápidamente y a bajo costo, gracias a su amplia gama de materiales de impresión 3D, proporciona una alternativa excepcional a los procesos de fabricación tradicionales para fabricar componentes personalizados. Con sede en Wisconsin, STS Technical Group ha estado operando durante casi 40 años trabajando con clientes en diseño técnico y la dotación de personal y desafíos de ingeniería. Con más de 250 empleados en los centros de contratación en los EE. UU., La empresa ha crecido y se ha adaptado al panorama en constante cambio de las tecnologías de fabricación, ofreciendo servicios nuevos e innovadores a medida que surgen.
STS utiliza la tecnología de impresión 3D de Formlabs debido a la variedad de materiales que son adecuados para un uso extensivo en el entorno de fabricación, la capacidad de producir componentes impresos en 3D de grado médico y la alta calidad de los componentes impresos. En este caso de estudio, el Director de Servicios de Ingeniería de STS Technical Group, Benjamin Heard, lo guía a través del desarrollo de pinzas personalizadas para mover y colocar inyectores de combustible en un entorno de fabricación, destacando las ventajas de imprimir en 3D vs a producirlo con métodos de producción tradicionales como la fundición y mecanizado. Heard también explicará por qué las capacidades de las pinzas impresas en 3D personalizadas son muy superiores a las pinzas anteriores fabricadas tradicionalmente. Ver info
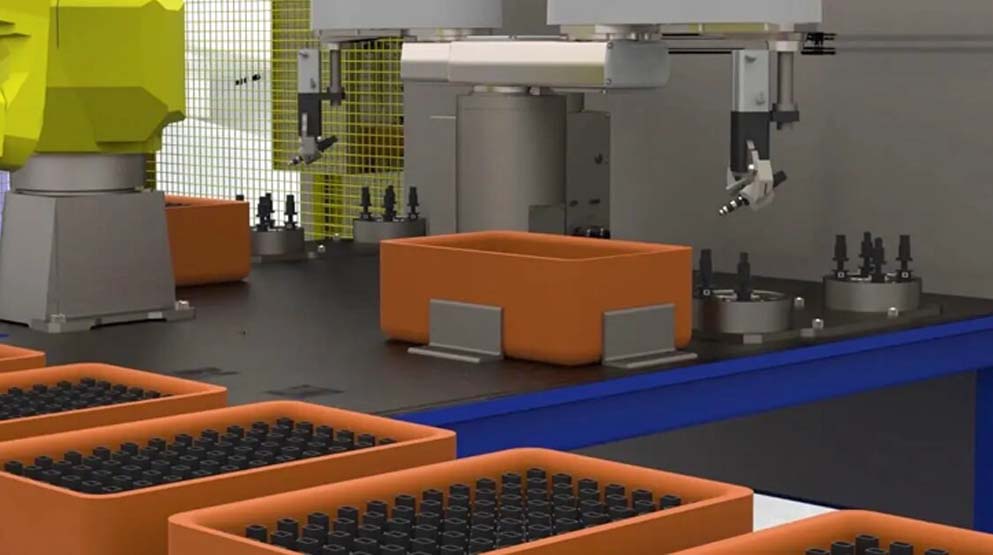
Cómo elegir un proceso de producción para componentes específicos
Para fabricar un componente específico, se deben considerar muchos procesos de producción durante el desarrollo, como procesos de fundición, fabricación, mecanizado e impresión 3D como el modelado por deposición fundida (FDM) o la impresión estereolitográfica (SLA) .
Algunas ventajas de la impresión 3D para la fabricación de componentes:
- Mayor detalle que la fundición y / o el mecanizado. El grosor de la capa de impresión puede ser tan pequeño como 25 micrones.
- Más rentable que la fundición, la fabricación o el mecanizado cuando se trata de diseños muy detallados.
- Tiempos de producción y producción significativamente más bajos que los de fundición, fabricación o mecanizado.
- No se requiere mecanizado después de la impresión, por lo tanto, no hay necesidad de tener costosos equipos de mecanizado que requieran mano de obra calificada y una tediosa configuración.
Al decidir entre componentes de fundición, fabricación, mecanizado o impresión 3D, primero considere la durabilidad que debe poseer la pieza. Si bien las piezas metálicas producidas con procesos tradicionales ofrecen mayor resistencia, durabilidad y resistencia al desgaste, muchos componentes tienen requisitos que pueden satisfacerse fácilmente mediante la impresión 3D con materiales de ingeniería específicos. El entorno de trabajo también debe tenerse en cuenta durante la selección para garantizar que el material pueda soportar la temperatura, los niveles de humedad o la presencia de corrosivos. La impresión 3D de componentes grandes puede representar un desafío, pero las impresoras 3D de gran formato, como la formlabs form3 , pueden adaptarse a solicitudes de impresión más grandes.
Diseño e impresión en 3D de pinzas de inyector de combustible personalizadas
Se tienen en cuenta muchos factores al diseñar pinzas para operaciones de recogida y colocación. Los materiales utilizados en el componente recogido y la pinza, la fuerza de agarre, la geometría del componente recogido, las mordazas radiales frente al movimiento lineal de la mordaza, las holguras circundantes y las tolerancias de ubicación de recogida y colocación requeridas. El material de los dedos de la pinza se selecciona típicamente para que sea significativamente más fuerte y más duro que la pieza recortada para garantizar que los brazos no se desgasten después de miles o incluso millones de ciclos. Un material de agarre típico es el acero endurecido, que puede dañar las superficies de las piezas recogidas más blandas. Cuando el acabado es delicado, se agregan revestimientos o zapatos a las pinzas. Además, cuando las piezas se mueven a su posición para realizar trabajo adicional de la máquina en el artículo, un mal contacto de agarre podría resultar en una mala colocación de la pieza y la creación de defectos mecanizados.
La fabricación del componente de uso final requería un material más duradero para sostener el entorno de producción. Como resultado, se utilizó la resina Rigid 4000 para hacer las pinzas finales. Este material de polímero relleno de vidrio extremadamente rígido ofrece una gran durabilidad, rigidez y un acabado atractivo para las piezas impresas
Resultados
El proceso de diseño e impresión 3D de las pinzas irregulares fue un completo éxito y funcionan como se esperaba. Las capacidades de las pinzas impresas en 3D son muy superiores a las de las pinzas anteriores.
Add comment